Limpeza de Gás de Alto Forno
Limpeza de Gás de Alto Forno
O processo de produção de ferro líquido no alto-forno (BF) gera gás no topo do forno que é um importante subproduto do processo de BF. Este gás de topo do alto-forno está na temperatura e pressão existentes no topo do BF e geralmente contaminado com poeira e partículas de água. Este gás de topo tem um valor calorífico substancial e é conhecido como gás BF bruto ou gás BF contaminado. A composição e quantidade deste gás de topo dependem da natureza do processo tecnológico no alto-forno e do tipo e qualidade das matérias-primas utilizadas para a produção de ferro no alto-forno. A fim de usar ainda mais o gás BF bruto, é necessário limpá-lo usando certos sistemas de processo que reduzem seu teor de partículas sólidas.
O gás de topo contém monóxido de carbono (CO) e é conhecido como gás de alto-forno após sua limpeza. É usado como gás combustível para aquecer o ar de sopro nos fogões de sopro quente, bem como combustível suplementar na usina siderúrgica. Para que o gás BF seja utilizado como gás combustível, é necessário que o gás BF bruto seja limpo e resfriado para reduzir os volumes de gás e o teor de umidade. O resfriamento prévio e a redução do volume de gás também são necessários, pois resultam em economias substanciais nos custos de entrega em todo o extenso sistema de distribuição da siderúrgica.
A análise típica do gás de alto-forno para um alto-forno operando com injeção de carvão pulverizado (PCI) é fornecida na Tab 1. Os sistemas de processo para a limpeza do gás são sistema de limpeza de gás úmido ou sistema de limpeza a seco. Os sistemas de limpeza de gás de alta eficiência são vitais para a operação confiável e longa vida útil do sistema de jateamento a quente de alta temperatura do BF, bem como da rede de gás BF na usina siderúrgica. O sistema de limpeza úmida é o sistema mais comumente usado para a limpeza do gás BF.
Guia 1 Análise típica de gás BF com PCI | ||
Constituinte | Unidade | Valor |
CO | % Vol. | 20 – 24 |
CO2 | % Vol. | 18-23 |
H2 | % Vol. | 1,5-4,5 |
N2 | % Vol. | 52-57 |
SO2 | mg/cum | 10-30 |
NH3 | mg/cum | 5-21 |
Cloreto | mg/cum | 50-200 |
Óxidos de N2 | mg/cum | 3-12 |
A principal função do sistema de limpeza de gás do alto-forno é remover o material particulado desse gás. Além disso, o sistema também resfria o gás para reduzir seu teor de umidade, aumentando assim seu poder calorífico. O lodo/poeira recuperado contém quantidades relativamente altas de ferro e carbono e, portanto, pode ser reciclado através da planta de sinterização.
O conhecimento do processo do alto-forno é necessário para o projeto e operação adequados do sistema de limpeza de gás. A preparação da carga e o tipo de carga de minério (pellet ou sinter) afetam a quantidade e o tamanho das partículas do pó. Além disso, a escolha e preparação de materiais fundentes afetam a química da água no sistema de lavagem. O cálcio pode ser introduzido no sistema de água a partir do calcário usado como agente fundente. Os injetores de coque e combustível contribuem com enxofre, cloretos, amônia e óxidos de nitrogênio. A análise do gás varia com os materiais de carga e operação do BF com ou sem PCI. O nível de produção e as taxas de vento afetam as cargas de partículas no sistema de limpeza de gás.
A pressão de topo e a queda de pressão do lavador (no caso de sistemas úmidos) afetam a eficiência da coleta de poeira, bem como a adsorção de gases dissolvidos na água do lavador. Além das funções básicas de limpeza e resfriamento do gás de topo, o purificador e/ou a turbina de recuperação de energia do gás de topo também controla a pressão de topo do alto-forno. Para uma operação suave e estável do forno, a pressão máxima deve ser controlada e mantida o mais constante possível. O projeto do sistema de limpeza de gases deve, portanto, ser totalmente integrado à operação do alto-forno.
Durante operações como carregamento, rosqueamento, equalização e troca de fogões, ocorrem inevitavelmente variações no fluxo e pressão do gás. As flutuações são geralmente de curta duração, mas de amplitude considerável e são sentidas no topo do alto-forno, bem como a jusante em todo o sistema de gás. O sistema de limpeza de gás BF deve ser projetado para lidar e controlar tais flutuações.
O gás BF que sai do topo do forno em caso de forno operando com PCI contém cerca de 20-30 gramas de pó de combustão por metro cúbico normal de gás e não pode ser usado como tal. Este pó contém partículas finas de coque, materiais de carga e compostos químicos que se formam devido às reações que ocorrem no alto-forno. A distribuição típica de tamanho de partícula no gás BF bruto com o uso de PCI é fornecida na Tab 2.
Guia 2 Distribuição típica do tamanho de partícula em gás BF bruto com PCI | |||
Classe | Tamanho da partícula em micrômetros | Tamanho médio em micrômetros | % de distribuição |
1 | 0-10 | 5 | 9 |
2 | 11-30 | 20 | 8 |
3 | 31-60 | 45 | 12 |
4 | 61-100 | 80 | 17 |
5 | 101-200 | 150 | 17 |
6 | 201-400 | 300 | 17 |
7 | 401-600 | 500 | 10 |
8 | 601-800 | 700 | 10 |
Como o objetivo principal da limpeza do gás de alto-forno é produzir gás refrigerado e livre de poeira para ser usado como combustível nos fornos da siderurgia, o sistema de limpeza de gás deve ser projetado para atender a esse objetivo.
A remoção eficaz de uma mistura de poeira grossa e fina de um gás muito empoeirado requer o uso de um coletor de poeira e um sistema de lavagem multiventuri. O resfriamento eficaz requer o uso de uma torre de resfriamento de gás antes da descarga do gás BF na rede de gás BF na usina siderúrgica. O gás BF bruto é limpo na planta de limpeza de gás em dois estágios, a saber, estágio primário de limpeza de gás e estágio secundário de limpeza de gás. O fluxograma típico do sistema de limpeza de gás de alto-forno é mostrado na Fig 1.
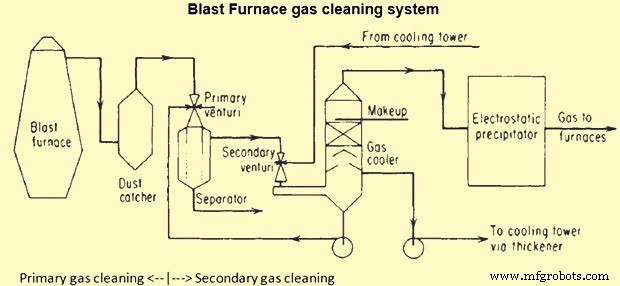
Fig 1 Folha de fluxo do sistema de limpeza de gás
Estágio primário de limpeza de gás
A limpeza primária de gás é baseada no princípio de separação por gravidade e é usada para a remoção de grandes partículas de poeira. É a separação a seco de partículas de poeira no gás de topo do alto-forno antes da lavagem úmida e é comumente feita por um coletor de poeira por gravidade ou mais recentemente por ciclones de grande diâmetro. Nesta etapa todas as partículas mais grossas são removidas. O objetivo é remover o máximo de poeira possível em uma condição seca para reutilização e reciclagem. O pó reciclado também deve ter baixo teor de zinco e levar a satisfazer os limites do balanço de zinco do alto-forno. A eficiência de remoção de poeira do separador depende da distribuição do tamanho das partículas, do mecanismo de separação (ou seja, força gravitacional ou centrífuga) e, em menor grau, da carga de poeira de entrada. O pó separado é normalmente de tamanho superior a 10 micrômetros e é coletado na tremonha de armazenamento de pó, que geralmente é dimensionado para um dia e meio de acúmulo de pó, e esvaziado por meio de um sistema de descarga de pó.
O coletor de pó é uma grande estrutura cilíndrica normalmente com um grande diâmetro e com a altura necessária. Geralmente é forrado para isolá-lo e evitar a condensação da umidade no gás BF para que o pó permaneça seco e não enrole e escoe livremente na porção cônica do coletor de pó em sua parte inferior para sua remoção periódica.
O gás é enviado para o coletor de pó por um único canto inferior e entra pela parte superior por um tubo vertical que transporta o gás para baixo dentro do coletor de pó. Este tubo se alarga em sua extremidade inferior como um funil invertido, de modo que, à medida que o gás desce, sua velocidade (e, portanto, seu potencial de transporte de poeira) diminui, e a maior parte da poeira mais grossa cai do fluxo de gás e é depositada no cone em na parte inferior do coletor de poeira. Como a parte inferior do coletor de poeira está fechada e a saída de gás está próxima ao topo, a direção do deslocamento do gás deve reverter 180 graus. Essa reversão repentina na direção do fluxo faz com que mais poeira se assente.
A operação e a eficiência de um coletor de pó por gravidade convencional são regidas pela lei de Stokes. Em 1851, George Stokes derivou uma expressão para a força de atrito (também chamada de força de arrasto) exercida em objetos esféricos com números de Reynolds (Re) muito pequenos, por exemplo, partículas muito pequenas, em um fluido viscoso contínuo, resolvendo o limite de massa de fluido pequeno das equações de Navier-Stokes geralmente insolúveis.
No entanto, a lei de Stokes só é aplicável a objetos esféricos com números de Re muito pequenos com velocidades de sedimentação na região laminar. Para partículas com números de Re superiores a 0,2 e até 100.000, o grau de turbulência torna-se significativo, levando a uma força de arrasto adicional. Assim, a velocidade de sedimentação (ou terminal) é geralmente menor do que a prevista pela lei de Stokes. Para esses tamanhos de partículas, a velocidade terminal é determinada pela correlação entre o número Re da partícula e seu coeficiente de arrasto usando os valores fornecidos nas tabelas Haywood. Alternativamente, a correlação entre a partícula Re e o número de Arquimedes (Ar) (válido entre Re =0,2 e 20.000) pode ser usada.
Se as partículas estão caindo em um fluido viscoso por seu próprio peso, então uma velocidade terminal, também conhecida como velocidade de sedimentação, é alcançada quando essa força de atrito combinada com a força de empuxo equilibra exatamente a força gravitacional. Com base na lei de Stokes combinada e nas tabelas de Haywood, a velocidade terminal de cada grupo de partículas pode ser determinada. A partir da velocidade terminal da partícula pode ser calculada a eficiência de remoção, que depende da velocidade ascendente do gás no anel coletor de pó e, portanto, do diâmetro do barril.
No caso do coletor de pó tipo ciclone, a operação e a eficiência do coletor de pó são baseadas em forças centrífugas. No coletor de pó do ciclone, o gás bruto do alto-forno é introduzido por uma ou duas entradas tangenciais com uma velocidade para forçar as partículas de pó para a parede e separá-las do fluxo de gás. O coletor de pó ciclone pode ter diferentes tipos de construção interna. Um tipo de ciclone está completamente vazio, enquanto outro tipo tem uma cúpula de entrada complicada e palhetas-guia substituíveis.
A maior separação de poeira dentro do ciclone está ligada às forças centrífugas e às altas velocidades circunferenciais dentro do ciclone em comparação com a tecnologia de coletor de poeira. As velocidades mais altas no interior da embarcação requerem uma proteção especial das superfícies dentro da embarcação. Um coletor de pó é muitas vezes operado sem qualquer proteção das superfícies internas devido à baixa velocidade do gás, mas a tecnologia de ciclones exige uma proteção dessas superfícies para evitar o desgaste.
O coletor de pó ciclone é geralmente com localizador de vórtice, ápice, cone de fluxo e um funil de coleta de pó com saída dupla de pó. A eficiência de coleta do ciclone depende muito da distribuição do tamanho das partículas. Partículas abaixo de 5 micrômetros não são removidas devido à sua pequena massa; partículas entre 5 micrômetros e 30 micrômetros são parcialmente separadas e partículas maiores que 30 micrômetros são completamente separadas no coletor de pó cônico. A eficiência geral de separação do coletor de pó de ciclone é melhor do que o coletor de pó por gravidade. A poeira seca removida contém muito pouca concentração de zinco e chumbo e pode ser facilmente reciclada. O coletor de pó ciclone reduz a carga de pó no estágio secundário que consiste na limpeza de gás úmido.
O coletor de poeira está equipado com um sistema de descarga de poeira para despejar o pó em lotes abaixo da pressão atmosférica para evitar o acúmulo de poeira no coletor de poeira e reduzir as emissões de poeira e gases. O pó é geralmente umedecido antes de ser descarregado no solo ou diretamente em um dumper/vagão abaixo. Existem dispositivos de detecção de nível instalados na tremonha de pó para indicação de nível. Os sinais dos dispositivos de detecção de nível são usados para monitorar o acúmulo de poeira, iniciar o ciclo de despejo de poeira e fornecer alarmes de nível baixo e alto.
Estágio secundário de limpeza de gás
O gás BF após a limpeza primária no coletor de pó, onde a maioria das partículas pesadas são removidas, passa para a etapa de limpeza secundária do gás (depuradores) que é o sistema de limpeza úmida. Nesta etapa, o gás BF é limpo em contato com a água e quase todas as partículas suspensas são separadas (mais de 99%). Em algumas plantas, este gás é ainda levado para precipitadores eletrostáticos. O gás tratado após a etapa secundária de limpeza de gás é levado para a rede de gás BF da planta e é usado também para aquecimento de fogões BF. A água poluída do sistema, ao mesmo tempo, contém altas concentrações de partículas suspensas na faixa de 500-10.000 mg/le, como tal, é enviada para lagoas de decantação/clarificador-espessante onde a poeira se assenta e a água limpa do topo é bombeado para reutilização. Os depuradores estão disponíveis em uma ampla variedade de designs, tamanhos e capacidades de desempenho. Eles devem ser projetados principalmente para coleta de partículas.
A operação sem problemas do depurador, mesmo durante condições difíceis de acionamento do forno, é um pré-requisito para a produção econômica de ferro no alto-forno. O design do purificador deve ser otimizado para fornecer alta confiabilidade e desempenho superior. As características necessárias do purificador são (i) múltiplos mecanismos de remoção de poeira, (ii) requisitos mínimos de água de lavagem, (iii) controle de pressão superior superior, (iv) desempenho comprovado e alta eficiência, (v) baixa necessidade de espaço, (vi) baixo consumo de energia e (vii) baixa emissão de ruído.
O tamanho das partículas é um dos fatores mais importantes que afetam a eficiência de remoção do purificador. As partículas maiores são muito mais facilmente removidas, enquanto as partículas submicrônicas são as mais difíceis de remover.
Com relação ao mecanismo de remoção de poeira no lavador úmido, a separação das partículas de poeira do gás do alto-forno requer a aplicação de uma força que produz movimento diferencial da partícula em relação ao gás e tempo de retenção suficiente para a partícula migrar para o superfície coletora.
Os depuradores para a limpeza de gases de alto-forno operam com base no princípio aerodinâmico básico. Uma analogia simples do princípio aerodinâmico é que, se gotículas de água de tamanho muito grande forem projetadas para colidir com partículas de fluxo de gás de tamanho muito menor, as chances estatísticas de colisão são muito pequenas. À medida que o tamanho das gotículas de água é reduzido para mais próximo do tamanho das partículas do fluxo de gás, as chances de colisão aumentam. Estudos mostraram que um filme de superfície ao redor de uma gota de água tem uma espessura aproximada de 1/200 de seu diâmetro. Uma partícula de corrente de gás em voo flui através do filme aerodinâmico ao redor da gota sem colisão se ela tiver um diâmetro menor que 1/200 do diâmetro da gota de água. Mas se o diâmetro da gota de água for muito menor, a colisão ocorreria. Uma partícula de mira de 10 mícrons requer gotas de água menores que 2000 mícrons (200×10) para coleta adequada. A depuração eficiente, portanto, requer a atomização da água até uma finura relacionada ao tamanho das partículas para proporcionar o máximo contato com as partículas a serem capturadas. Além disso, a probabilidade de uma gota de água atingir as partículas de poeira é proporcional à concentração de poeira. É menos provável que uma única partícula de poeira atinja uma única gota do que um enxame delas. Para equalizar esses fatores, os depuradores são regulados quanto ao volume de gás a ser lavado (medido pela queda de pressão da corrente de gás) e água a ser pulverizada (medida pela pressão hidráulica nos bicos de pulverização). A altura e o diâmetro da câmara de depuração também são adaptados às características conhecidas do gás.
Os principais mecanismos de separação na lavagem de gases de alto-forno consistem em (i) interceptação inercial, (ii) difusão turbulenta (Browniana) e (iii) interceptação da linha de fluxo. Quando uma pequena partícula é suspensa em um fluido, ela é submetida ao impacto das moléculas do líquido. Para partículas ultrafinas (colóides), o momento instantâneo transmitido à partícula varia aleatoriamente, o que faz com que a partícula se mova em um caminho erótico agora conhecido como movimento browniano. A interceptação inercial é caracterizada pelas diferentes forças inerciais das massas variáveis. Quando o gás carregado de poeira flui ao redor da gota de água coletora, as partículas de poeira de massa maior não seguem as linhas de fluxo do fluxo de gás. Essas partículas, impulsionadas pela força de inércia, atingem e penetram na gota de água e, assim, são removidas da corrente de gás. A difusão turbulenta é altamente eficaz na remoção de partículas menores de poeira do fluxo de gás. Partículas pequenas, particularmente aquelas abaixo de cerca de 0,3 micrômetros de diâmetro, exibem um movimento browniano considerável e não se movem uniformemente ao longo da corrente de gás. Essas partículas se difundem da corrente de gás para a superfície das gotículas de água e são coletadas. Este mecanismo de coleta só pode funcionar em depuradores que promovem fluxo turbulento de uma mistura gás-líquido, operam em baixa velocidade e proporcionam tempo de retenção suficiente. A interceptação da linha de fluxo só funciona se a linha de gás passar dentro de um raio de partícula da gota de água coletora. A partícula de poeira que viaja ao longo dessa linha de corrente toca a gota de água e é coletada sem a influência da inércia ou difusão turbulenta. Os mecanismos de remoção de poeira durante a lavagem com água do gás BF são apresentados na Fig 2.
Fig 2 Mecanismos de remoção de poeira
O coletor de pó é meramente uma câmara de decantação para remover partículas grandes e reduzir a carga sobre os lavadores de venturi. O gás passa por um venturi primário (com separador) e um venturi secundário para uma remoção de partículas ainda mais eficaz. Em seguida, o gás passa pela combinação separador de arraste/torre de resfriamento de gás. O gás limpo e resfriado é então enviado para a rede de gás BF da siderúrgica. O resfriamento adequado é necessário para reduzir o nível de umidade do gás para evitar problemas nas linhas de distribuição de gás BF e nos fornos.
A água reciclada coletada no primeiro venturi, contendo alto teor de particulados, é enviada diretamente para um clarificador-espessante. A água reciclada coletada do separador é recirculada para o primeiro lavador venturi. A água de reposição é adicionada ao clarificador e o transbordamento combinado é reciclado para o venturi secundário. Assim, a água mais limpa entra em contato com o gás mais limpo e volta para o primeiro venturi e depois para o clarificador. A água pode ser reciclada do espessante para o purificador ou pode ser usada para algum outro propósito, como têmpera de escória.
Uma torre de resfriamento convencional é normalmente usada para remoção de calor da água da torre de resfriamento de gás ou água do purificador. O projeto da torre permite manter a água de resfriamento e a água do lavador venturi separadas. A água do depurador geralmente contém dureza e alcalinidade consideráveis dos finos de cal na carga no alto-forno. Consequentemente, a escala é frequentemente encontrada. Depósitos de óxido de ferro e carbono não queimado também são uma preocupação em muitos sistemas. Os problemas de deposição são mais frequentemente encontrados nos bicos de venturi primários e na região da garganta, onde o gás contém o maior nível de particulados, e nas linhas e bombas indo e vindo do espessador.
No entanto, a deposição pode ocorrer em qualquer um dos depuradores venturi, nos separadores, na torre de resfriamento de gás ou nas linhas e bombas de reciclagem do depurador. A clarificação é outra área de grande problema, uma vez que a separação inadequada de líquidos/sólidos resulta em baixa qualidade da água do transbordamento do clarificador.
Recentemente, nos altos-fornos recém-construídos e reconstruídos, particularmente na República Popular da China, a limpeza a seco de gás de alto-forno por filtros de manga encontrou ampla aplicação. A limpeza a seco com gás tem as seguintes diferenças em relação à limpeza com gás úmido com depuradores venturi.
- A ausência de água no processo de limpeza elimina ou reduz uma série de instalações hidráulicas do alto-forno, por exemplo:estação de bombeamento de lodo do sistema de limpeza de gás, tanques de decantação de lodo e floculadores, estação de bombeamento para transferência de polpa, estação de bombeamento de circulação do ciclo de retorno do gás limpeza, etc.
- A temperatura do gás após a limpeza está na faixa de 100°C a 120°C, que é 50°C a 70°C mais alta do que a temperatura do gás após a limpeza com gás úmido. Além disso, a umidade do gás é reduzida em 50 a -60 gramas/cum, que juntos equivalem a um aumento no valor calórico do gás de alto-forno em 50 a 60 kcal/cum.
- Redução do teor de poeira no gás de alto-forno para 2-3 mg/cum que melhora a vida útil dos fogões a quente e também melhora o desempenho da turbina de recuperação de alta pressão.
- Melhoria ambiental na siderúrgica devido a uma melhor remoção de poeira do gás e eliminação das instalações de manuseio de lodo.
O sistema de limpeza de gás secundário baseado em limpeza a seco consiste no seguinte.
- A unidade de filtro de mangas com várias seções, em cada uma delas estão instaladas algumas dezenas de mangas filtrantes
- Sistema de sacos de pulso de limpeza de poeira por nitrogênio
- Suporte e proteção de estruturas metálicas
- Sistemas de dutos de gás com válvulas e compensadores de efeito térmico
- Sistema de limpeza e reciclagem de pó capturado (pneumático ou com transportadores raspadores)
- Sistema de fornecimento de nitrogênio para a purga do filtro e para o transporte pneumático de poeira
- Sistema de alívio de pressão do filtro de mangas
- Unidade de armazenamento de poeira capturada
- Sistemas de automação, inspeção e controle elétrico
O filtro de mangas normalmente possui de 8 a 16 seções, que são dispostas em duas fileiras, onde uma ou duas seções estão em stand-by, mais uma seção está no modo de limpeza de nitrogênio de purga cíclica e outras seções estão no modo de limpeza de gás. Para o material filtrante, é utilizado um tecido com alta resistência ao desgaste, refratário, etc. Além disso, após o tratamento químico, o tecido é fácil de limpar do pó durante a limpeza de purga, uma vez que melhorou as propriedades de repelência à água e ao óleo. O tecido também evita a ocorrência de corrente eletrostática. A taxa máxima de filtragem é de 1,0 a 1,5 cum/minuto e a temperatura do gás é de 50 graus C a 280 graus C (o sistema também pode operar de forma estável (confiável) por 2 horas na temperatura do gás de 300 graus C).
O teor normal de poeira do gás de alto-forno após a limpeza geralmente não é superior a 3 mg/cum. A vida útil dos sacos de tecido é geralmente de até dois anos.
Processo de manufatura
- Geração e uso de gás de alto-forno
- Uso de Nut Coke em um Alto Forno
- Sistema Básico de Recuperação e Limpeza de Gás de Forno de Oxigênio
- Injeção de carvão pulverizado em um alto-forno
- Irregularidades do alto-forno durante a operação
- Sistema de resfriamento do alto-forno
- Sistemas de carregamento de alto-forno
- Química da Ferragem por Processo de Alto Forno
- Revestimento refratário do alto-forno
- Injeção de gás de forno de coque em um alto-forno