A fórmula perfeita para alinhar operações e manutenção
Quando as operações e a manutenção não funcionam bem juntas, pode ser caro. E bagunçado. Veja a história de um fabricante de alimentos como exemplo.
A instalação usa uma folha, que rola enormes bolas de massa. A lâmina precisa ser limpa todos os dias. A equipe de produção limpa regularmente a máquina com água. Há apenas um problema com isso - a água faz a massa se aglomerar e quebrar a máquina. Como resultado, a manutenção de emergência é a norma.
Se esta situação parece familiar para você, você não está sozinho. Isso acontece milhares de vezes ao dia. Operações e manutenção têm objetivos, motivações e processos diferentes. O resultado é confusão, frustração e acusações. Isso não é bom para os negócios ou para a saúde dos funcionários.
Este artigo é sobre como quebrar esse ciclo e melhorar o alinhamento entre operações e manutenção, incluindo:
- Métricas para compartilhar
- Como aumentar a colaboração
- Dicas para construir processos conjuntos
Por que alinhar as operações e a manutenção deve ser sua prioridade
Qualquer fabricante que esteja trabalhando para reduzir o desperdício está liderando o grupo ou prestes a sair do campo. Para provar isso, basta olhar para o fato de que os fabricantes desperdiçam 20% de cada dólar que gastam.
O desperdício costuma aparecer durante a produção, conforme destacado por estas estatísticas assustadoras (cortesia de Automation.com):
- Grandes instalações industriais perdem mais de 323 horas de produção por ano devido ao tempo de inatividade não planejado
- O custo médio anual de paralisação é de $ 532.000 por hora ou $ 172 milhões por planta
- O custo do tempo de inatividade para os fabricantes da Fortune 500 é igual a 8% da receita anual
Custos enormes são uma coisa. Mas atrasos no trabalho, manutenção reativa e compras de emergência também têm um preço mental e físico.
Melhorar a relação entre operações e manutenção é fundamental para reduzir o tempo de inatividade em sua origem.
“Quando a manutenção e as operações estão alinhadas, permite que a empresa encontre problemas dentro das operações”, afirma Jason Afara, engenheiro de soluções sênior da Fiix.
“E então os líderes de negócios podem tomar decisões informadas sobre como corrigir esses problemas com os recursos apropriados. Transforma jogos de adivinhação e jogos de culpa em um esforço unificado. ”
Onde alinhar as operações e os processos de manutenção
Planejando o tempo de inatividade programado
A definição de manutenção eficiente é manter o equipamento em pleno funcionamento com o menor tempo de inatividade possível. Claro, isso é mais fácil dizer do que fazer. A equipe de produção tem cotas a preencher. Qualquer coisa que atrapalhe esse alvo é uma ameaça. Isso inclui manutenção.
“Combatíamos as operações apenas para obter um pouco de manutenção em uma máquina”, diz Jason, lembrando-se de sua época como gerente de manutenção.
Isso é muito comum e improdutivo. Felizmente, há duas maneiras de a manutenção e as operações criarem um plano de manutenção preventiva que beneficie os dois grupos:
- Use os dados para comparar o impacto da manutenção com o impacto da falha
- Desenvolva processos compartilhados que reduzam a quantidade de tempo de inatividade programado
O primeiro passo é para que ambas as equipes entendam como suas atividades afetam o desempenho dos equipamentos. Mais uma vez, muitas vezes é mais complicado do que parece.
“É aqui que os departamentos de manutenção geralmente falham”, diz Charles Rogers, consultor de implementação sênior da Fiix com mais de 33 anos de experiência em manutenção.
“Eles não têm dados para fazer backup de suas solicitações. Você tem que ser capaz de provar seu caso e mostrar evidências de que, se você não fizer a manutenção dentro do prazo, haverá consequências muito piores em algum ponto - provavelmente mais cedo ou mais tarde. ”
A melhor maneira de alinhar seus esforços é determinar o risco aceitável e as consequências do fracasso como uma equipe. Compartilhe informações sobre modos de falha comuns, com que frequência se espera que ocorram, bem como tempos de reparo e custos para cada um. Compare isso com a frequência da manutenção programada, o tempo que leva para fazer essas tarefas e os custos envolvidos.
Quantificar a diferença deixa claro que programar pausas frequentes na produção para manutenção é a melhor maneira para ambas as equipes atingirem seus objetivos e evitar interrupções grandes e demoradas.
Use este modelo FMEA para calcular o risco de falha e priorizar a manutenção
A criação de processos compartilhados entre operações e manutenção permite que as equipes compartilhem dados de ação. Por exemplo, permite que os operadores detectem pequenas falhas e os técnicos de manutenção respondam a elas com mais rapidez. Exemplos desses processos incluem:
- Reuniões regulares entre os líderes de operações e manutenção para discutir a produção e os cronogramas de manutenção preventiva, mudanças nas especificações das máquinas ou outras atualizações
- Reuniões trimestrais entre as duas equipes para discutir sucessos, desafios, soluções e análise da causa raiz
- Um processo de solicitação de trabalho que permite aos operadores de máquina identificar problemas com rapidez e confiança e capacita os técnicos a priorizar e responder aos problemas com o mínimo de interrupção
Criação de trabalho compartilhado e responsabilidades claras
Qualquer menção de operações e manutenção trabalhando juntas levará inevitavelmente a falar de manutenção produtiva total (TPM). Você pode ler uma pequena cartilha sobre TPM aqui, mas a ideia é que todos em uma empresa (desde técnicos a contadores) são responsáveis e envolvidos na manutenção.
Tornar as operações parte do processo de manutenção é uma das maneiras mais fáceis e eficazes de começar a construir um programa TPM. Aqui está um exemplo de como isso pode ser feito:
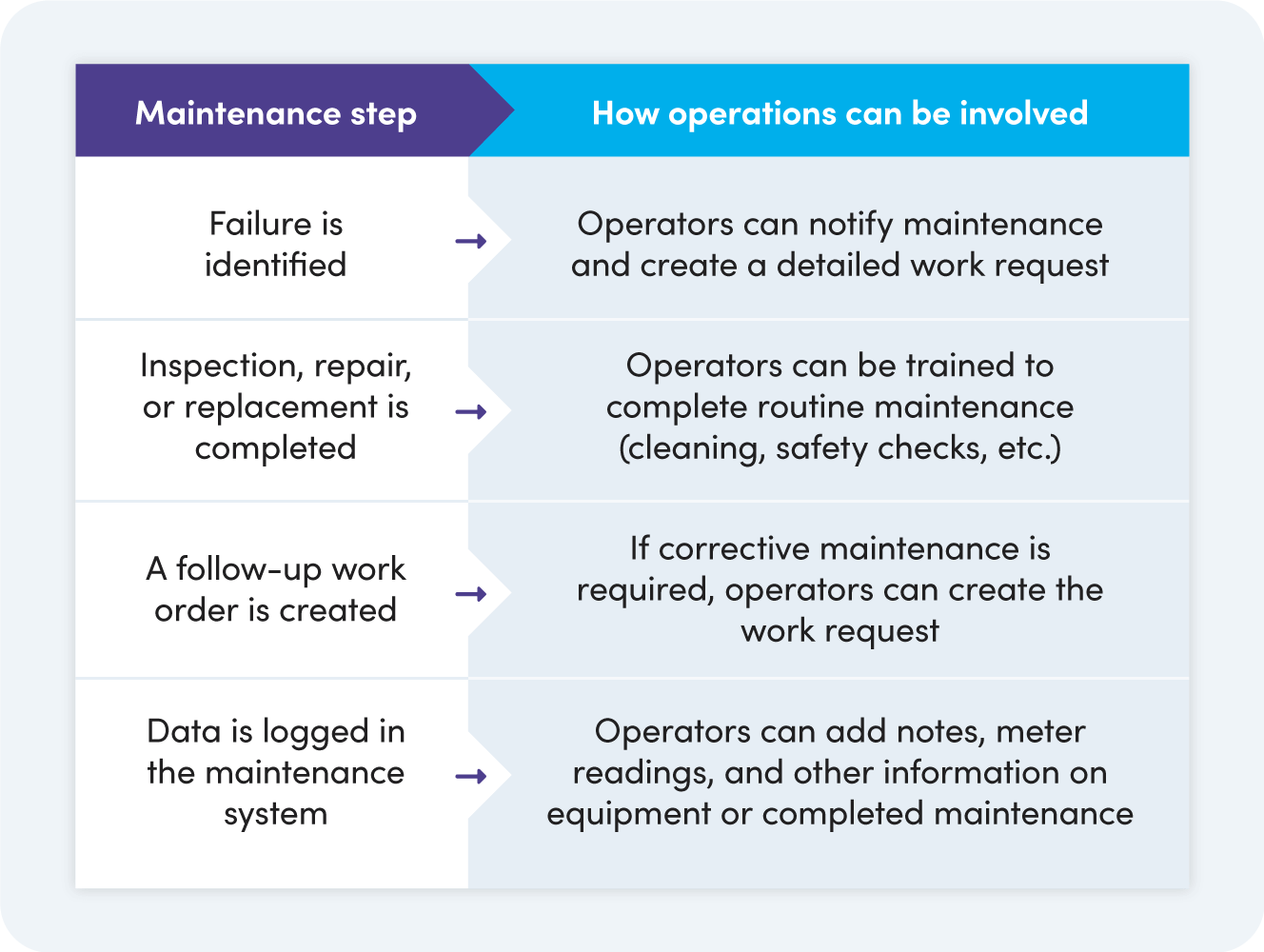
12 maneiras de usar ordens de serviço para iniciar seu programa TPM
A chave para tornar esses processos compartilhados bem-sucedidos é criar responsabilidades de trabalho claras. Quando as pessoas sabem exatamente o que precisam fazer, isso ajuda você a:
- Forneça o treinamento e os materiais certos para as pessoas certas
- Crie cronogramas e orçamentos precisos
- Teste novos processos, otimize-os e expanda-os
- Escolha dados inválidos e descubra a causa raiz deles
Comece definindo responsabilidades claras criando um tipo de manutenção para os operadores. Isso permite que você acompanhe quanto trabalho está dando às operações. Também ajuda a projetar modelos de ordens de serviço para os operadores, para que eles saibam o que fazer e aonde ir se o escopo do trabalho mudar.
Criação de cronogramas de trabalho realistas
Quando as operações e a manutenção sabem quanto tempo leva para fazer as coisas, é mais fácil definir cronogramas, orçamentos e metas de acordo. Também evita atrasos invisíveis, reduz a frustração e estimula o respeito entre as duas equipes. Mas não é útil compartilhar cronogramas de manutenção se eles não forem precisos. Existem algumas estratégias para garantir que as expectativas correspondam à realidade:
- Observe os registros de manutenção do equipamento. Identifique o trabalho que frequentemente leva mais tempo do que o esperado e ajuste os cronogramas de acordo.
- Analise os dados de sua ordem de serviço para encontrar PMs com uma alta taxa de manutenção de acompanhamento necessária. Inclua isso em suas instruções para a equipe de operações.
- Responsável por partes de uma ordem de serviço que estão fora do tempo real da chave inglesa. Isso inclui a recuperação de peças, a conclusão de procedimentos de segurança e a execução de testes em máquinas.
Fornecer cronogramas realistas nem sempre significa que seus horários serão compatíveis. Mas ajuda operações e manutenção a ter uma conversa sobre o que pode ser feito no tempo que você tem. Ao determinar qual manutenção pode ser sacrificada para a produção, aqui estão algumas perguntas a serem feitas:
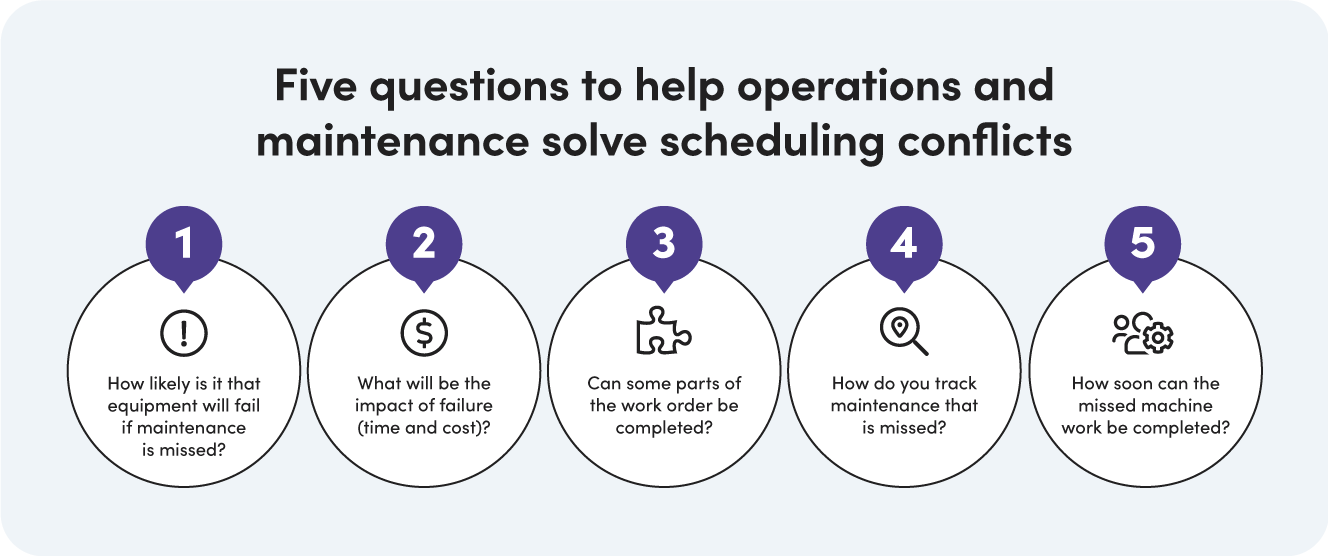
Cinco maneiras de construir um relacionamento forte entre operações e manutenção
Suas equipes de operação e manutenção podem ser melhores amigas. Ou talvez haja alguma tensão entre eles. Seja qual for o relacionamento, sempre há uma oportunidade de torná-lo melhor com algumas estratégias simples.
Crie várias maneiras para as duas equipes se comunicarem
A comunicação com outras equipes costuma ser uma das primeiras atividades a ser abandonada quando o trabalho fica agitado. É por isso que deve haver processos formais em vigor para manter o fluxo de informações. A criação de canais dedicados para comunicação pode incluir:
- Reuniões de equipe:reuniões regulares criam espaço para que a voz de todos seja ouvida e para manter os desafios, planos e atualizações visíveis
- Canais para postar e ver atualizações:podem ser qualquer coisa, desde um quadro branco a um grupo WhatsApp ou um portal de solicitação de trabalho digital para rastrear o status das solicitações
- Revisões por pares:este é um processo em que os membros da equipe de operações e manutenção revisam uns aos outros anonimamente para identificar como eles podem trabalhar melhor juntos
Existem algumas informações importantes para discutir quando você estiver trabalhando nesses canais:
- Atualizações de máquinas:traz mudanças de especificações, problemas potenciais, riscos de segurança ou atualizações para procedimentos operacionais padrão
- Cronogramas:Fale sobre os próximos trabalhos, riscos ou conflitos, o que é necessário para ter sucesso e quaisquer mudanças em relação ao que foi discutido anteriormente
- Relatórios:analise as metas, o progresso, as tendências problemáticas ou os principais sucessos em seus relatórios
- Roadblocks e soluções:discuta os principais desafios ou dúvidas de sua equipe e colabore em maneiras de remover esses obstáculos
- Planejamento de longo prazo:descubra como ambas as equipes podem melhorar continuamente, incluindo como gerenciar melhor os orçamentos, atingir as metas de longo prazo e desenvolver novas habilidades
Ter uma estrutura de comunicação entre as operações e a manutenção permite que você transforme a conversa em ação. Aqui estão algumas regras básicas:
- Concentre-se nas soluções, não na culpa:encontrar uma solução deve ser o objetivo de todas as suas conversas
- Concentre-se no coletivo:encontre soluções que funcionem para todos, em vez de tentar ganhar uma discussão ou batalha para sua equipe
- Desenvolva um ciclo de feedback:crie confiança emitindo feedback e mantendo todos cientes do progresso
- Valorize a consistência, mas seja flexível:comprometa-se a se comunicar, mas entenda que as reuniões podem ser deslocadas de vez em quando, caso ocorra uma emergência
- Crie uma agenda para todas as reuniões:tenha um plano para o que vai falar, para que possa aproveitar ao máximo o tempo de todos
Defina as mesmas metas
Haverá menos atrito entre as operações e a manutenção quando as duas equipes definirem o sucesso da mesma forma. Pode haver idéias diferentes sobre como chegar ao seu objetivo, mas os dois departamentos irão na mesma direção.
“Na pior das hipóteses, esses departamentos são irmãos que estão constantemente lutando”, diz Jason.
“Mas, na melhor das hipóteses, vocês estão trabalhando juntos para atingir os mesmos objetivos, comemorando juntos quando atingem essas metas e juntando forças para voltar aos trilhos quando não o fazem.
Existem algumas métricas pelas quais as operações e a manutenção podem compartilhar a responsabilidade:
- Arranques limpos após a manutenção e rendimento na primeira passagem / boa na primeira passagem:ambos os números visam medir a eficiência e o desperdício
- Custo total por unidade de produção:tanto as operações quanto a manutenção podem ser responsáveis pela redução de custos e, ao mesmo tempo, pela melhoria da qualidade
- Tempo gasto apoiando a produção / manutenção:rastrear o tempo que cada equipe gasta apoiando a outra ajudará você a alocar recursos e criar planos de contratação eficazes
- Tempo de inatividade não planejado (últimos 90 dias):veja o impacto da manutenção preventiva e os processos compartilhados que tornam este trabalho eficiente
- Tempo médio para detectar e reparar:todos têm a participação de encontrar e consertar as falhas antes que elas causem falhas e com o mínimo de interrupção possível para os negócios
Use este modelo para criar metas compartilhadas entre operações e manutenção
Integrar sistemas de produção e manutenção
É fácil para as operações ter uma visão negativa da manutenção quando sua única exposição é uma avaria ou interrupção do serviço. Integrar os sistemas usados para produção e manutenção fornece visibilidade sobre o trabalho de cada equipe. Isso permite que você veja o impacto positivo de cada departamento e ajude um ao outro a realizar ainda mais.
A equipe de manutenção de Ryan Robinson é um grande exemplo de como a integração do software de manutenção com equipamentos e sistemas de produção pode entregar resultados incríveis. Ryan, o gerente de loja de um produtor de árvores no atacado, conectou sensores em várias máquinas com um CMMS. Isso deu a ele os dados de que precisava para otimizar os intervalos de manutenção e aumentar a eficiência da produção.
“Como sabemos como o equipamento é usado diariamente, temos uma ideia do que se espera da manutenção amanhã, no dia seguinte e no dia seguinte”, diz Ryan.
Ryan também foi capaz de usar esses dados para detectar veículos com muitos tempos de inatividade. Ele trouxe essa informação ao gerente da fazenda, que descobriu o motivo e encontrou uma solução.
Leia a história de Ryan
Equipes de manutenção de classe mundial estão alinhadas com as operações
Operações e manutenção são o coração de qualquer empresa com muitos ativos e grandes metas de produção. É por isso que é essencial que eles desenvolvam um relacionamento saudável e processos formais para trabalharem juntos. As duas equipes devem compartilhar tudo, desde as métricas que almejam aos sistemas que usam e a programação que orienta seu trabalho. A união de forças lhes dá melhor visibilidade dos desafios que os negócios enfrentam e o poder de superá-los. É uma situação em que todos ganham.
Manutenção e reparo de equipamentos
- Caneta e papel vs. software de manutenção:O melhor método para reduzir o tempo de inatividade
- Navegando na modernização da manutenção e gestão de instalações
- Qual é a cura para a manutenção não planejada?
- Compartilhe a responsabilidade pela obtenção da manutenção preventiva
- Uma lição de direção para operações e manutenção
- A necessidade de programação de manutenção
- O esforço multi-habilidades para manutenção
- 5 Regras para operações e manutenção de parceria
- Lockheed Martin adjudicou contrato de operação e manutenção
- Como os anos 2010 mudaram a indústria de manutenção e as previsões para o que vem a seguir