Como desenvolver e implementar processos de manutenção melhores
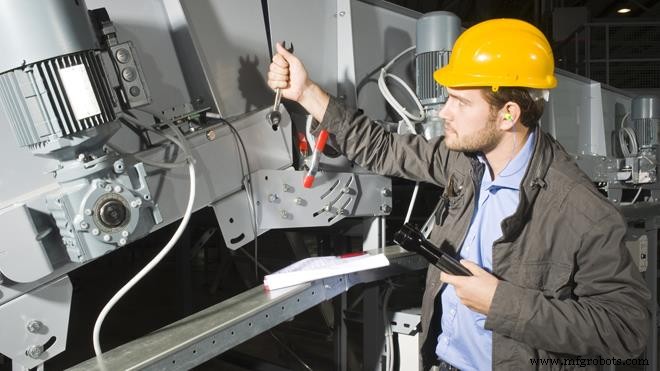
Ao longo desse tempo, trabalhei como um millwright da linha de frente, planejador / planejador, supervisor, gerente de projeto, gerente de manutenção e agora gerente sênior. Tendo trabalhado em tantas funções e setores em combinação com o treinamento de desenvolvimento profissional, adquiri muito conhecimento quando se trata de desenvolver e implementar programas de manutenção enxutos e confiáveis.
Não é sempre que surge a oportunidade de realmente colocar sua impressão digital em uma organização. Durante a fase de entrevista, o diretor da Gold Bar me deixou bem claro que eles queriam alguém que conhecesse os processos. No primeiro dia de trabalho, basicamente me disseram:“Você não foi contratado com base na sua aparência, então vamos ver o que você tem na sua mala de truques”. Obviamente, estou apenas brincando, mas fiquei bem ciente da grande oportunidade que estava diante de mim.
Em 18 de dezembro de 2017, assumi minha função atual como gerente sênior. Este artigo irá detalhar nossa jornada nos últimos 19 meses e como estamos caminhando para alcançar a excelência em manutenção.
Em primeiro lugar, gostaria de compartilhar a melhoria que vimos em três indicadores-chave de desempenho (KPIs) de dezembro de 2017 a novembro de 2018.

Também quero deixar claro que recebo muito pouco crédito por esses números. Como todos sabemos, o ativo mais importante para qualquer empresa são as pessoas. Sem todos no Gold Bar puxando a corda na mesma direção, isso não teria sido possível.
Além das pessoas, outros fatores-chave incluem estratégia, gestão do trabalho, gestão de materiais, processos e sistemas de suporte. A seguir está uma breve sinopse do que descobri em cada uma dessas áreas quando cheguei, bem como como melhoramos as coisas.
Pessoas
Steven R. Covey disse uma vez:“Você pode comprar a mão de uma pessoa, mas não pode comprar seu coração. Seu coração está onde está seu entusiasmo, sua lealdade. Você pode comprar suas costas, mas não pode comprar seu cérebro. É aí que está sua criatividade, sua engenhosidade, sua desenvoltura. ”
Tive a sorte de o cavalheiro que substituí ter resolvido 95% dos problemas de recursos humanos. Entrei em um grupo de pessoas engajadas, ávidas por processos e por serem melhores no que fazem.
Enquanto eu continuava a descascar camadas da cebola, logo percebi que havia colaboração multifuncional ocorrendo em certos níveis e que não havia muito trabalho de silo acontecendo.
Quando se trata de pessoas, a coisa mais importante que você pode fazer como líder é construir a confiança de sua equipe. Capacite seus funcionários a tomar decisões e aceite o fato de que eles tomarão decisões erradas de vez em quando. Pegue-os, espane-os e coloque-os de volta na estrada na direção certa. Certifique-se de ter uma conversa com eles para que entendam perfeitamente que precisam aprender com os erros quando eles acontecerem.
Henry Ford disse:“Mesmo um erro pode acabar sendo a única coisa necessária para uma realização que valha a pena.”
A maior satisfação que tenho em liderar uma equipe engajada é contar a eles minha visão e, em seguida, sair do caminho deles. Remova os bloqueios de estradas e deixe-os voar alto.
Estratégia
Quando comecei na Gold Bar, a estratégia era manter a fábrica funcionando, o que em si não é uma estratégia ruim de se ter, mas a que custo? A fábrica tem 50 anos e a cultura já existe há algum tempo. Eu não iria mudar durante a noite, nem sabia o que precisava ser mudado. Passei os primeiros dois meses analisando os processos atuais, conversando com qualquer pessoa que pudesse sobre manutenção, incluindo membros da equipe de manutenção, pessoal de operações, engenharia, etc.
Fiz uma análise de lacunas e observei tudo, desde nosso pessoal e gestão de trabalho até gestão de materiais e processos. Fiquei agradavelmente surpreso que Gold Bar tinha uma forma muito básica de todos os principais processos de manutenção. Eles tinham um esqueleto, uma estrutura, mas precisávamos colocar um pouco de carne nos ossos.
Para ter uma melhor noção de onde estávamos no momento, olhei para o ciclo de vida de uma ordem de serviço, desde o momento em que foi inserida em nosso sistema informatizado de gestão de manutenção (CMMS) como uma solicitação de trabalho até que o trabalho fosse executado e o processo de encerramento concluído. Em outras palavras, como era nossa gestão de trabalho? Mais uma vez, fiquei agradavelmente surpreendido por haver um padrão de gestão do trabalho, embora não fosse muito robusto.
Pelo menos eles haviam pensado nisso, e o conceito não era estranho para eles. Toda a ideia de gerenciamento de trabalho não era apenas "fazer com que fosse feito!" Havia um fluxograma de linha única que tinha algumas caixas de decisão em torno do trabalho emergente, planejamento e execução, então tínhamos um ponto de partida.
Embora os documentos de gerenciamento de trabalho carecessem de qualquer substância real, a manutenção ainda estava sendo executada de forma eficaz. Houve uma grande comunicação entre as operações e a manutenção, e as coisas correram bem.
Dito isso, não havia muita importância na proteção do cronograma de manutenção, e muitas negociações ocorreram na linha de frente entre os encarregados de operações e os encarregados da manutenção. Eu tinha que ter cuidado como isso era tratado, pois a última coisa que eu queria era corromper esse relacionamento.
Gestão de Materiais
Quando comecei a mergulhar em nosso gerenciamento de materiais, percebi rapidamente que havia uma oportunidade considerável para melhorias. Tínhamos um grande estoque gerenciado pelo fornecedor de luvas, óculos de segurança, baterias, fita adesiva etc. que era gratuito e nos custava muito dinheiro. Não tínhamos como rastrear peças sobressalentes renováveis, então havia pilhas de esquilos por toda parte.
Como a manutenção centrada na confiabilidade (RCM) e o modo de falha e análise de efeitos (FMEA) nunca foram realizados, não sabíamos se tínhamos as peças de reposição críticas certas no estoque. A cultura era manter o estoque baixo. Os planejadores comprariam peças com cartões de crédito em vez de criar números de estoque e utilizar o gerenciamento da cadeia de suprimentos (SCM). O espaço no armazém era limitado e não o estávamos fazendo uso eficaz. Também não tínhamos kits ou encenação.
Processos
Enquanto alguns processos careciam de manutenção, a segurança era bem gerenciada. Gerenciamento de mudanças, gerenciamento de segurança de processos, registro de perigos e procedimentos de trabalho seguro foram de primeira linha. Mais uma vez, fiquei satisfeito por termos um grupo engajado de funcionários que levava a segurança a sério. Mostrou em suas estatísticas, com apenas uma lesão registrável em 2017 e uma em 2018. Considerando o nível de engajamento, eu sabia que não seria difícil desenvolver os processos.
Sistemas de suporte
Nosso programa CMMS tem muita potência, mas estávamos utilizando apenas uma pequena parte de sua funcionalidade. Também tínhamos maneiras muito complicadas de inserir informações no sistema após a execução do trabalho. Os comerciantes escreveriam notas à mão na cópia em papel da ordem de serviço.
O capataz fecharia a ordem de serviço. A cópia impressa seria enviada ao administrador de manutenção, que por sua vez reabriria a ordem de serviço e digitaria as observações dos comerciantes no CMMS.
Também estávamos fazendo algum monitoramento baseado em condições. A análise do óleo estava sendo realizada externamente. As leituras de vibração foram coletadas pelos millwrights e analisadas pela engenharia, mas nenhum relatório foi criado ou dados correlacionados. Não houve esforço para identificar atores mal-intencionados ou desenvolver dados como tempo médio entre falhas (MTBF).
Abaixo estão algumas das conclusões da análise de lacunas:
-
Excelente força de trabalho - manteve o local funcionando
-
Mentalidade da velha escola a respeito de seguir os processos de gestão de trabalho
-
A programação de manutenção semanal foi criada na quinta-feira (três dias) antes de ser executada
-
Sem previsão formal de manutenção
-
Sem limpeza da carteira de manutenção
-
O trabalho de interrupção não foi baseado na criticidade do equipamento
-
Sem proteção de programação
-
Insuficiente entrada de dados no CMMS
-
Nenhuma estratégia formal para manutenção
-
Muitas peças compradas com cartões de crédito em vez de SCM
-
Má gestão de estoque, muitas pilhas de esquilo
-
Sem kits ou encenação
-
O armazém estava aberto e basicamente um sistema de honra
Como mencionado anteriormente, demorou 50 anos para chegar a este ponto, então não íamos fazer a volta com o navio durante a noite. Precisávamos definir metas pequenas e mensuráveis e caminhar antes de correr. Sempre que você implementa algo novo, é vital adiantar-se à mudança. A comunicação é de extrema importância.
Você deve comunicar a mudança à sua equipe o mais cedo possível, antes da implementação. Deixe-o penetrar, torne-se visível e disponível para responder a perguntas e dissipar qualquer medo. Certifique-se de que seus líderes estão na mesma página, porque se não é importante para quem lidera, não será importante para ninguém.
Todos reagem à mudança de uma maneira diferente. Uma das coisas mais importantes sobre a mudança é garantir que você tenha uma peça de sustentação integrada. Siga o modelo de W. Edwards Deming de planejar-fazer-verificar-agir. Monitore a mudança de perto e ajuste de acordo. Sem a peça de sustentação, muitas iniciativas de mudança fracassam e se tornam o sabor da semana.
Colhendo frutas perto do chão
A colaboração multifuncional e o debate construtivo e respeitoso que encontro diariamente não são encontrados em muitos lugares. Essas pessoas têm paixão por fazer a coisa certa. Tudo começa na reunião diária da equipe principal às 8h30. Esta é uma reunião multifuncional com representantes de operações, engenharia da planta, controles da planta, automação, engenharia de projeto e manutenção.
Todas as solicitações de trabalho que foram inseridas no CMMS nas últimas 24 horas são revisadas e priorizadas com base na designação de prioridade inserida na solicitação de trabalho. A data em que as operações gostariam de ter o equipamento de volta em serviço é inserida na solicitação. A data programada para execução será revisada assim que o planejamento for concluído e o trabalho for preparado e preparado.
O desafio era fazer com que as pessoas se concentrassem na criticidade do equipamento. Se o ativo não for crítico para a operação da planta, ele não deve entrar no cronograma. Tive que reforçar com os encarregados da manutenção que eles precisavam proteger o cronograma. Imediatamente, começamos a ver mudanças nos KPIs de trabalho break-in e de conformidade do cronograma.
O planejamento e a programação foram os próximos. Você pode ter certeza de que o cronograma será concluído ao desenvolvê-lo em uma quinta-feira, uma semana antes da execução do trabalho? Sem garantir que todos os trabalhos fossem preparados e encenados, eu tinha pouca confiança. No entanto, eles ainda tinham 70% de conformidade com o cronograma, o que achei razoável.
Tive uma reunião com minha equipe de liderança e implementamos uma programação contínua de cinco semanas. Agora travamos o cronograma de manutenção semanal 10 dias antes da execução. Embora a programação esteja bloqueada com 10 dias de antecedência, ela é revisada na reunião de programação semanal para garantir que as prioridades da planta não tenham mudado e que todos os trabalhos tenham sido preparados e preparados. Se todas as peças necessárias não estiverem equipadas para o trabalho, elas serão removidas da programação.
Também instituímos parâmetros para a forma como gerenciamos o trabalho emergente ou invasivo. Esta foi uma das principais mudanças para aumentar nosso desempenho de manutenção preventiva (PM). Na reunião principal, se houvesse trabalho emergente, a primeira coisa a ser excluída do cronograma era a manutenção corretiva de baixa prioridade, depois os PMs e, por fim, o trabalho que exigia um isolamento mais extenso.
Junto com o treinamento de desenvolvimento profissional que concluí ao longo da minha carreira, também fiz muitos trabalhos com sistemas enxutos. Portanto, sempre que procuro fazer mudanças, faço isso com uma mentalidade enxuta. Estou sempre tentando eliminar o desperdício do processo e acredito piamente em apenas fazer trabalho com valor agregado.
A próxima área que abordamos foi a manutenção preventiva. Havia muito pouca manutenção realizada com base nas condições. A maioria dos PMs era baseada no tempo. Expliquei a curva P-F para nosso pessoal e disse que realizar PMs é vital para nos mover do combate a incêndios para a prevenção de incêndios.
A frequência também é muito importante. Se estivermos fazendo PMs semanais, mas não houver nenhuma mudança, podemos precisar liberar algumas horas de trabalho, mudando a frequência para duas semanas e assim por diante. Na última metade de 2018, modificamos mais da metade de nossos 1.400 PMs. Vimos um aumento dramático na conclusão de PM e na quantidade de solicitações de trabalho que refletiam "trabalho corretivo de PM".
Ao longo dos últimos nove meses de 2018, focamos no desenvolvimento do nosso processo de gestão do trabalho. Agora está bastante detalhado. Nosso lema para 2018 era “fazer a manutenção certa na hora certa”. Com essa mentalidade, temos tido muito sucesso. Em retrospecto, o que realmente fizemos? Analisamos as solicitações de trabalho de uma lente diferente com base na criticidade do equipamento para a operação.
Priorizamos a forma como o trabalho foi executado para que houvesse ênfase na conclusão de PMs. Fizemos alterações na reunião de agendamento semanal para antecipar cinco semanas e bloqueamos o cronograma de manutenção semanal 10 dias antes da execução. Implementamos kits e encenação. Tudo o que estava no cronograma de manutenção que estava por vir precisava ser equipado e preparado.
Agora temos reuniões quinzenais de revisão de conformidade do cronograma com os encarregados da manutenção. Assim que iniciamos essas reuniões, vimos um grande aumento no cumprimento do cronograma. Os encarregados da manutenção sabiam então que eram responsáveis pelo cronograma e eram seus donos.
Também criamos uma classe de sub-estoque em nosso CMMS para que as peças recondicionáveis pudessem entrar em estoque com um valor associado que seria cobrado de um ativo quando fosse usado.
Além disso, as pessoas foram responsabilizadas. Acredito firmemente que todos têm um balde de trabalho a fazer, desde a pessoa na ponta de uma mangueira até o CEO, e você deve trabalhar em seu próprio balde.
Para onde ir a partir daqui?
Agora que conhecemos o básico, adicionaremos lentamente novas coisas para melhorar continuamente. Fornecemos treinamento a todos os funcionários de manutenção para que eles pudessem inserir todas as suas descobertas diretamente no CMMS e concluir suas tarefas. Estamos começando a implementar códigos de falha no CMMS para que possamos rastrear por que o equipamento está falhando e identificar os malfeitores.
Escolhemos quatro funcionários de manutenção para ser nosso grupo de monitoramento baseado em condições. Este ano, vamos treiná-los em análise de vibração, teste ultrassônico, termografia e tribologia. O objetivo é ter uma equipe de manutenção especializada e autossuficiente em quatro anos.
Em dezembro, realizamos um curso de treinamento de RCM de três dias, do qual participaram 17 funcionários da Gold Bar. Isso nos permitiu revisar todos os nossos sistemas usando o modelo RCM e garantir que temos as estratégias certas para nossos ativos, que eles são atribuídos com a criticidade correta e que temos os componentes sobressalentes críticos em estoque.
Nossa estratégia mudou. No final de 2021, o Gold Bar fará a transição de uma organização de manutenção reativa e preventiva para um departamento de manutenção preventiva e sob condição. Compartilhar a nova estratégia e visão com a equipe e todos os membros da família Gold Bar ajuda a manter todos focados. Se eles souberem o objetivo, eles nos ajudarão a construir o plano.
Este artigo foi publicado anteriormente na Reliable Plant 2019 Conference Proceedings.
Manutenção e reparo de equipamentos
- Software de manutenção preventiva de decodificação:O que ele faz e como usá-lo
- 12 modelos de manutenção e como usá-los
- Como construir e otimizar um cronograma de manutenção preventiva
- Como criar um planejamento de manutenção eficaz e parceria de depósito
- Manutenção e confiabilidade - bom o suficiente nunca é
- Como implementar a manutenção produtiva total
- Como justificar um investimento em manutenção e confiabilidade
- Melhor prevenir do que remediar:Como melhorar a saúde e segurança com software de manutenção
- 4 barreiras para adotar software de gerenciamento de manutenção (e como superá-las)
- Como melhorar a saúde e a segurança na fabricação