Um guia ridiculamente simples para gerenciar o tempo de inatividade planejado | Inatividade programada
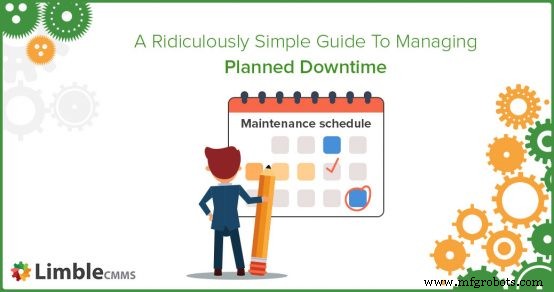
A manutenção preventiva é a estratégia de manutenção mais popular porque traz muitos benefícios e, ao mesmo tempo, não é incrivelmente difícil ou cara de implementar.
Dito isso, a manutenção preventiva tem suas desvantagens.
Uma das objeções mais citadas é que implementá-lo significa que você estará fazendo uma manutenção excessiva. Em outras palavras, seus técnicos perderão tempo com inspeções desnecessárias e ativos que podem (ainda) não exigir esse nível de atenção.
Se cavarmos um pouco mais fundo, veremos que isso nos leva a uma questão mais significativa. Quando você está fazendo um trabalho preventivo em um ativo, em muitos casos, esse ativo precisa ser encerrado primeiro. Na tradução, você precisa agendar o tempo de inatividade planejado.
Como ninguém quer desligar um ativo durante os horários de pico de produção ou para trabalho de manutenção que ainda não precisa ser feito, vamos ver como você pode desenvolver um cronograma de manutenção que leve em consideração esses desafios e minimize os tempos de parada programados.
O que é tempo de inatividade planejado | tempo de inatividade programado?
Simplificando, o tempo de inatividade planejado é um período de tempo que você reserva para manutenção programada e atualizações durante o qual seus ativos devem ser desligados.
Uma vez que a manutenção proativa é frequentemente feita em ativos críticos que são importantes para a produção, você não tem outra solução a não ser pausar as operações normais de produção até que os reparos / inspeções / atualizações sejam feitos.
As organizações procuram evitar esses problemas programando a manutenção durante os turnos noturnos (ou outros horários em que as máquinas não estão em uso). No entanto, se o seu departamento de manutenção não trabalha em turnos noturnos ou se você tem um ciclo de produção 24 horas por dia, 7 dias por semana, encontrar o momento certo para programar o tempo de inatividade planejado pode ser muito complicado, muito rápido.
Observação rápida:no restante do artigo, usaremos os termos “tempo de inatividade planejado” e “tempo de inatividade programado” alternadamente, pois se referem à mesma coisa na prática.
Inatividade planejada e não planejada
A diferença entre o tempo de inatividade planejado e não planejado é autoexplicativo:VOCÊ decide quando quer ter um tempo de inatividade planejado, MÁQUINAS decide quando querem fazer uma pausa e não se preocupam em perguntar se isso se encaixa na sua programação.
Piadas à parte, falhas inesperadas de equipamento que levam a tempo de inatividade não planejado podem ser muito caros , que é um dos principais motivos pelos quais muitas empresas estão mudando de manutenção reativa para preventiva .
Saber quanto tempo você gasta em manutenção planejada versus não planejada é essencial, portanto, é uma das muitas coisas que Limble mantém controle para você.
Aqui está um exemplo de como você pode usar o Limble para rastrear quanto tempo você gasta em tarefas de manutenção planejada versus quanto tempo você gasta reagindo a problemas inesperados:

Vamos ver como agendar tempos de inatividade planejados para que você possa realizar a manutenção adequada com um impacto mínimo na velocidade e volume de produção.
Como gerenciar o tempo de inatividade planejado
# 1) Entenda sua produção
Ao longo do ano, é mais do que provável que você tenha um fluxo e refluxo na produção do dia a dia. Conheça cada máquina que você opera e discernir como as diferentes estações afetam os ciclos de produção e, por sua vez, o uso diário das máquinas.
Durante o pico de produção, planeje encontrar o melhor momento que afeta menos os resultados financeiros. Encontrar tempo para se preparar pode significar depois do expediente. Se você tem uma loja aberta 24 horas por dia, 7 dias por semana, isso pode significar o horário mais lento do dia.
A chave é saber quando a produção diminui e quando acelera de acordo com o planejado.
# 2) Reduza a manutenção excessiva com um CMMS
Uma das principais maneiras de executar um plano de manutenção bem-sucedido é ser capaz de organizar, gerenciar e rastrear grandes quantidades de informações em várias fontes.
Ter um CMMS moderno pode ajudá-lo muito a rastrear e dar sentido a todos esses dados.
Reduz a manutenção reativa em 73,2%
Veja os resultados que Red Hawk aprecia com Limble
Leia nosso
Estudo de caso
Aqui estão apenas algumas das coisas que você faz com um CMMS:
- registrar o desempenho da máquina e o histórico de ativos
- acompanhar o progresso de todas as tarefas (ler ordens de serviço)
- rastreie o uso de todo o estoque e peças sobressalentes
- acompanhar o desempenho do técnico
- programe e supervisione sua programação completa de manutenção preventiva
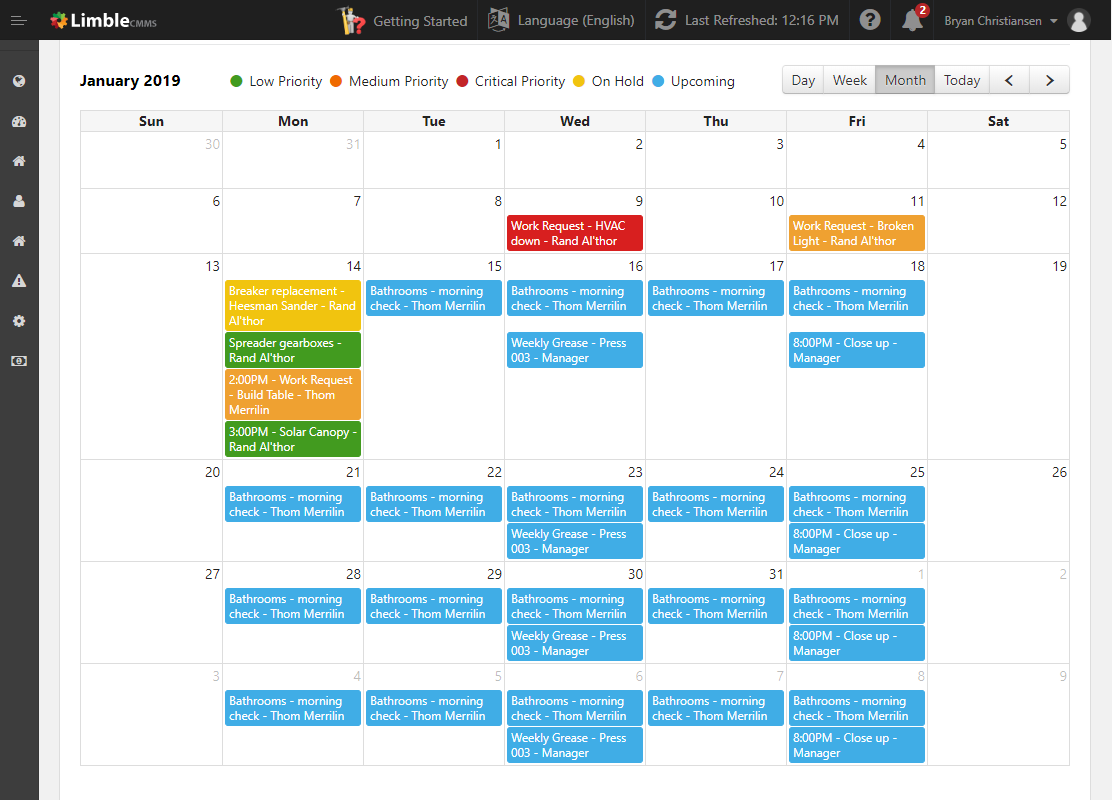
Ao ter todos esses dados à sua disposição, você pode reduzir a manutenção excessiva em :
- espaçamento da frequência do trabalho de manutenção em ativos que podem lidar com isso
- reduzir a duração do evento de tempo de inatividade, acelerando o diagnóstico e a comunicação da equipe
- garantindo que todas as peças sobressalentes estejam disponíveis quando você precisar delas
- ter um departamento de manutenção bem organizado em geral
Para uma análise aprofundada do CMMS, confira nosso guia O que é um sistema CMMS e como funciona.
# 3) Limite o foco de seu plano de manutenção
Uma ótima maneira de saber por onde começar sua programação de manutenção é listar todos os seus ativos e atribuir uma classificação a eles. Pode parecer óbvio, mas saber quais máquinas são de maior prioridade em sua fábrica lhe dará um norte.
Depois de listar suas máquinas importantes, liste os ativos menores que podem ser tão secundários que não precisam ser incluídos na manutenção de rotina.
As máquinas individuais, por exemplo, exigem menos esforço com o uso. Pode-se não precisar de óleo ou lubrificação; outro pode estar menos envolvido do que outros dispositivos, com muito menos peças móveis.
De qualquer forma, máquinas específicas precisam de menos manutenção geral. E deve ficar claro quais máquinas se enquadram nesta categoria. Afinal, muitas vezes não vale a pena ter todas as suas máquinas em um plano de manutenção preventiva.
Além de tudo o que foi mencionado, compreender quanto tempo cada tarefa de manutenção deve durar e quando a máquina é menos usada será crucial na criação de um plano de manutenção preventiva eficaz para que você possa programar o tempo de inatividade planejado no momento mais oportuno.
# 4) Ter um SOP claramente definido
Tendo claramente definido procedimentos operacionais padrão para cada operação que precisa ser repetida com frequência, é uma ótima maneira de agilizar suas operações de manutenção.
Como o tempo de inatividade planejado é algo que você terá que programar com razoável regularidade, ter diretrizes claras ajudará os técnicos a realizar seu trabalho com mais rapidez, o que significa que seus ativos precisarão de menos tempo para voltar ao trabalho.
Lembre-se de que a velocidade e qualidade do trabalho de manutenção executado são igualmente importantes . Embora seja bom manter o tempo de inatividade programado no mínimo, o trabalho de manutenção mal executado quase certamente levará a um aumento no tempo de inatividade não planejado.
E acho que todos podemos concordar que duas horas adicionais de paralisação programada são muito mais aceitáveis do que um dia inteiro de paralisação ou indisponibilidade não planejada.
# 5) Entenda seus gargalos
Atrasos frequentes na entrega tornam difícil manter um estoque de peças sobressalentes necessárias? Alguns técnicos de manutenção seniores se aposentaram ou deixaram a empresa, então você está trabalhando com uma equipe mais jovem que carece de experiência e treinamento? Você está trabalhando com ativos mais antigos que precisam de muita atenção e gostam de quebrar inesperadamente?
No contexto de minimizar o tempo de inatividade planejado para manutenção preventiva, peças de reposição , técnicos inexperientes / não qualificados e ativos antigos são os três gargalos mais comuns que você precisa programar.
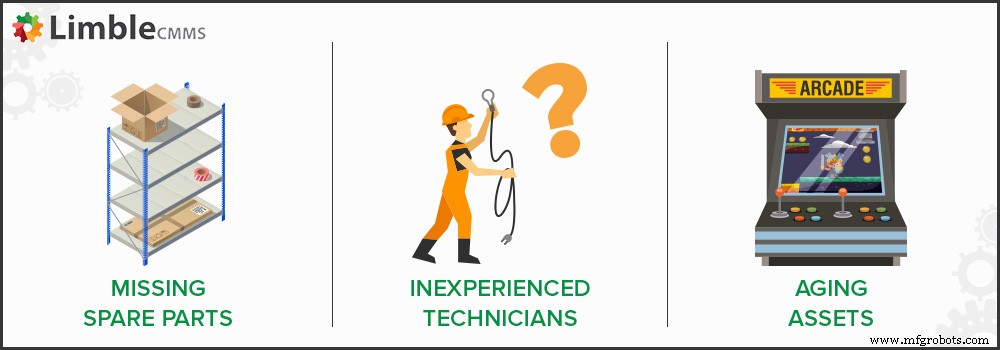
A boa notícia é que esses gargalos podem ser evitados com um pouco de solução alternativa e previsão.
Se suas peças de reposição não chegarem até você imediatamente, considere encomendá-las mais cedo ou mudar para um novo fornecedor, quando possível.
Quando você sabe que tem técnicos inexperientes, pode:
- junte-os a colegas mais experientes
- tem um SOP claramente definido de que acabamos de falar
- forneça a eles o treinamento necessário
- ter um processo de contratação mais rigoroso
E, por último, você deve encontrar uma maneira de contabilizar os ativos antigos. Na maioria dos casos, isso significa que você precisará prestar atenção especial a esses ativos, pois eles podem ser muito problemáticos e ser a causa de muitos períodos de inatividade não programados. Algumas maneiras de fazer isso são:
- rastreando cuidadosamente o histórico de ativos para extrapolar os padrões de decomposição comuns para que você possa tentar resolvê-los durante os tempos de inatividade planejados
- agendamento de inspeções adicionais que podem ser realizadas enquanto o ativo está em funcionamento
- instalação de sensores para realizar monitoramento com base na condição
# 6) Reduzir a duração dos tempos de inatividade programados por meio de colaboração efetiva
Os departamentos que interagem com o pessoal de manutenção devem estar na mesma página e coordenar ajustes e reparos de rotina. Contanto que todos entendam onde a equipe de manutenção estará para cada parada planejada, os operadores da máquina, equipe de limpeza e outros trabalhadores podem começar a preparar o ambiente para se concentrar apenas no que eles precisam fazer e garantir o mínimo de tempo de inatividade.
Quando ocorre o contrário, e há má comunicação entre os departamentos, não é difícil imaginar diferentes erros e acidentes que podem ocorrer e prolongar o tempo que seus ativos ficam em standby.
Não permita que a falta de organização e comunicação seja o motivo das paralisações planejadas causarem atrasos na produção.
Quando programar o tempo de inatividade planejado?
Como gerente de manutenção de instalações, é claro que só você pode encontrar o momento certo para programar o tempo de inatividade planejado em suas instalações.
Dito isso, temos algumas dicas que podem ajudar:
- Programe o trabalho de manutenção planejada após o horário comercial
- Imediatamente antes dos feriados principais
- Antes de um clima severo altamente antecipado
- Um a cada dois anos simule um apagão e teste todos os equipamentos críticos de uma vez
Para obter explicações mais detalhadas, você pode verificar minha postagem de convidado que discute quando agendar a manutenção planejada .
É tudo uma questão de planejar com antecedência
Como você pode ver, com planejamento e organização suficientes, você pode minimizar muito o tempo de inatividade durante a manutenção planejada.
Seja durante uma temporada de pico de produção ou na estação mais lenta do ano, estar organizado e ter um cronograma de manutenção exato irá garantir que sua produção seja executada no nível mais alto e que suas máquinas estejam em condições de operação de pico.
Se você estiver interessado em explorar totalmente como o Limble pode ajudá-lo a reduzir ao mínimo o tempo gasto em tempos de inatividade planejados, deixe um comentário abaixo ou envie-nos uma mensagem .
Manutenção e reparo de equipamentos
- Vs programado. Manutenção não programada em instalações de manufatura
- Um guia para implementação da manutenção produtiva total
- Guia para KPIs de Fabricação
- O futuro da manutenção:um guia prático para a Indústria 4.0
- Um guia simples para construir um programa de manutenção preditiva
- Manutenção baseada em condição:um guia completo
- A programação de manutenção precisa de um backlog planejado
- Um guia simples para benchmark de manutenção
- O que é manutenção programada?
- Guia básico para manutenção de minicarregadeiras